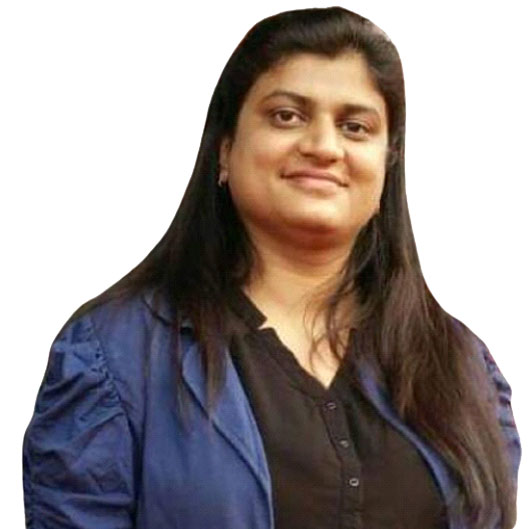
GEETIKA TIWARI
Is a Mechanical Engineer and an alumnus of IMT Ghaziabad. She did her PGDM with dual specialization in Operations & Marketing. A Quality Professional with an unmatched track record of 14 years in all the spheres of Quality and Quality Management System in the automotive / manufacturing industry.
A competent & result-oriented professional with an effective experience in devising significant solutions for day-to-day Quality Assurance, Quality Management System activities with focus on Customer Specific Requirements by ensuring optimal utilization of resources.
- Ability to see through the data on line to understand the variation and align actions to reduce variation in output or desired results.
- Quantum Improvement in internal rejection and scrap.
- Step Jump Improvement in Cost of Poor Quality / Cost of Quality.
- Continual self-sustaining actions post quantum jump to implement a system that's self-sustaining and aligning.
- Sustained and Improved Customer Rating / Ranking.
- New Product Development with Automotive customers like Maruti Suzuki India Limited, TATA Motors, General Motors, Volkswagen, Ashok Leyland & Nissan. And Non-Automotive customers like LG and Voltas.
Implement Organisation's Vision by Identifying Key Operational Metrics and build an MIS around them to steer a common direction while achieving yearly goals aligned to the Vision.
Highly resourceful at managing the entire functions of Quality Assurance and Certifications like: ISO 9001/ IATF 16949 / ISO 14001/ ISO 45001.
- Multiple organizational & statuary systems integrated into a single system to include all the aspects and deliver an Integrated Management Systems to synchronize and optimize the right balance looking at the key levers as decided by apex leadership.
- Understand Customer inputs for all interfaces across the organization to deliver a wholly responsive and aligned strategy back through all interfaces.
Possess sound expertise in Problem Solving; implementing measures for reduction of internal rejection and scrap in a structured manner.
- Ensuring basics / tools goes as a part of culture.
- Motivated and developed teams for Problem Solving.
- Teams won various awards for Quality Circle at ACMA, Quality Circle Delhi Chapter, ICQC etc.
A strong and firm approach to sustain and encourage safe work environments, and capabilities to streamline Quality indicators; applied continuous improvement principles to increase process efficiency and meet company budgets deadlines.